Tungsten carbide dies are an essential component in various industrial applications, particularly in metalworking and forming processes. Known for their exceptional hardness and wear resistance, these dies play a crucial role in ensuring the efficiency and productivity of manufacturing operations. However, over time, even the most robust carbide dies can experience wear and degradation. This blog post aims to provide a comprehensive overview of tungsten carbide dies and offer expert insights on how to enhance their service life.
What Are Tungsten Carbide Dies?
Tungsten carbide dies are precision-engineered tools used in the shaping, cutting, and forming of materials. Composed primarily of tungsten carbide, a compound known for its extraordinary hardness, these dies are capable of withstanding high levels of stress and temperature. Tungsten carbide is a composite material, meaning it is a combination of tungsten, carbon, and a metallic binder, usually cobalt or nickel. This composition grants carbide dies their exceptional properties, including:
High Hardness: Tungsten carbide is one of the hardest materials, ranking close to diamonds on the Mohs scale.
Wear Resistance: The material's durability ensures that it remains effective even after prolonged use.
Heat Resistance: Tungsten carbide can withstand high temperatures, making it suitable for demanding industrial processes.
Dimensional Stability: The material maintains its shape and size even under extreme conditions, ensuring consistent performance.
Factors Affecting the Service Life of Tungsten Carbide Dies
Several factors can influence the durability and effectiveness of tungsten carbide dies, including:
Material Composition: The quality of the tungsten carbide and the type of binder used can significantly impact the die's performance.
Manufacturing Process: Precision in the manufacturing process ensures that the dies meet the required specifications and performance standards.
Application Environment: The conditions under which the dies are used, such as temperature, pressure, and the nature of the materials being worked on, can affect their longevity.
Maintenance Practices: Regular maintenance and proper handling can prevent premature wear and extend the service life of the dies.
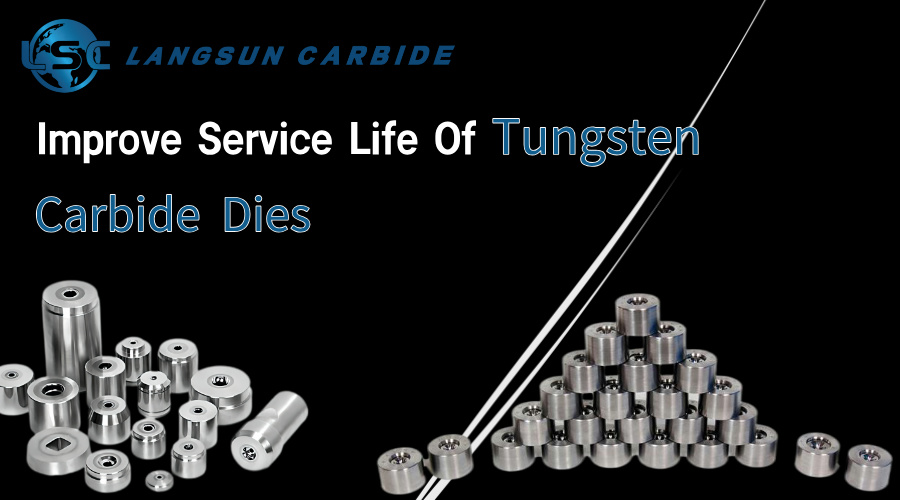
Tips to Improve the Service Life of Tungsten Carbide Dies
Choose the Right Grade of Carbide: Selecting the appropriate grade of tungsten carbide for your specific application can enhance performance. Different grades offer varying levels of hardness and toughness, so it's essential to choose one that matches your operational requirements.
Optimize Die Design: The design of the die should consider factors such as load distribution, stress concentration, and thermal management. Advanced design techniques, such as finite element analysis (FEA), can help in creating more efficient and durable dies.
Implement Proper Lubrication: Using the right lubricants can reduce friction and wear during the forming process. High-quality lubricants tailored to the specific application can significantly enhance the die's longevity.
Regular Inspection and Maintenance: Routine inspection and maintenance are crucial in identifying signs of wear or damage early. Regularly cleaning and re-sharpening the dies can also help in maintaining their effectiveness.
Control Operating Conditions: Monitoring and controlling the operating conditions, such as temperature, pressure, and speed, can prevent excessive wear and tear. Ensuring that the dies are not subjected to conditions beyond their design limits is essential for their durability.
Invest in Quality Materials: Using high-quality raw materials in the manufacturing process can result in superior tungsten carbide dies. Investing in reputable suppliers and conducting thorough quality checks can ensure the reliability and performance of the dies.
Tungsten carbide dies are invaluable in various industrial applications due to their exceptional properties. However, to fully benefit from their capabilities, it is essential to optimize their usage and maintenance. By selecting the right grade of carbide, optimizing die design, implementing proper lubrication, conducting regular maintenance, controlling operating conditions, and investing in quality materials, the service life of tungsten carbide dies can be significantly extended. These practices not only enhance the efficiency and productivity of industrial operations but also lead to cost savings and improved operational reliability.