Diamonds, renowned for their unparalleled hardness, have always demanded tools as robust as their own crystalline structure for cutting and shaping. Enter tungsten carbide blades—a marvel of modern materials engineering.
Understanding Tungsten Carbide: Composition and Properties
Tungsten carbide is a chemical compound comprising tungsten and carbon atoms in equal parts. This molecular structure imparts several critical properties making tungsten carbide an exceptional material for cutting tools:
Hardness: Tungsten carbide boasts a hardness level of about 9 on the Mohs scale, second only to diamonds. This high hardness enables the blade to cut through materials that other cutting tools cannot.
Wear Resistance: The durability and wear resistance of tungsten carbide extend the lifespan of cutting tools, making them cost-effective for long-term use.
Heat Tolerance: Tungsten carbide retains its hardness at elevated temperatures, which is crucial during high-speed cutting operations that generate significant heat.
Why Tungsten Carbide Blades Can Cut Diamonds
Despite the superlative hardness of diamonds, tungsten carbide blades can effectively cut through them due to several factors:
Microstructure: The fine-grained microstructure of tungsten carbide imparts a sharp, resilient cutting edge capable of engaging the diamond's lattice.
Bonding Strength: The strong covalent bonds within tungsten carbide resist deformation and maintain edge integrity when encountering the robust atomic structure of diamonds.
Precision Engineering: Advanced manufacturing processes enable the production of tungsten carbide blades with high precision, ensuring optimal performance in diamond cutting applications.
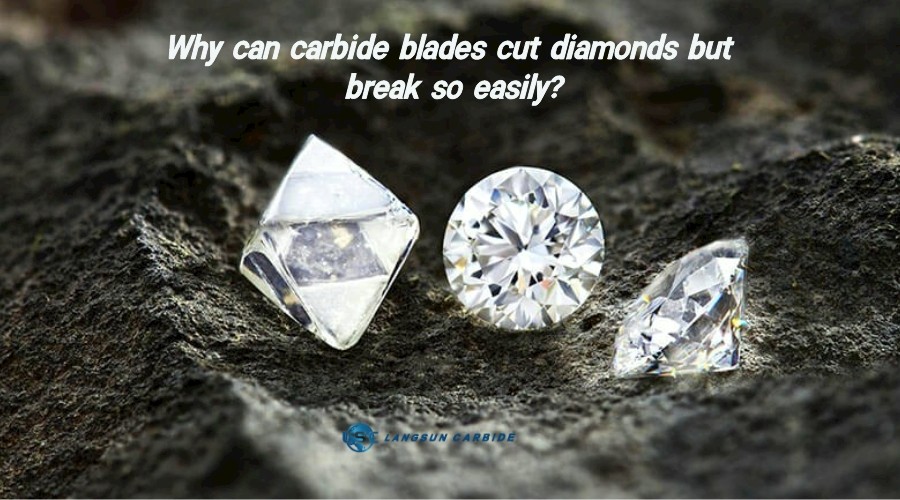
However, the very properties that make tungsten carbide blades extraordinary also make them susceptible to breakage. Understanding why these blades can fracture so readily is crucial for their effective application:
Intrinsic Brittleness: Tungsten carbide, while hard, is inherently brittle. Unlike more ductile materials, it lacks the ability to deform plastically. Therefore, when subjected to excessive force or improper handling, it can shatter.
Microcracks: During the cutting process, microcracks can develop in the blade. Over time, these microcracks may propagate, leading to blade failure.
Thermal Stress: Although tungsten carbide has excellent heat tolerance, rapid temperature fluctuations can induce thermal stress. If the thermal expansion is uneven, it can exacerbate pre-existing weaknesses and cause fracturing.
To optimize the longevity and efficacy of tungsten carbide blades when cutting diamonds, the following best practices are recommended:
Adequate Support: Ensure the blade is adequately supported and aligned to minimize stress concentration.
Controlled Cutting Speed: Maintain a controlled cutting speed to prevent excessive force and heat generation. This reduces the likelihood of microcracks and thermal stress.
Cooling Systems: Implement cooling systems, such as water jets or air blowers, to regulate the blade's temperature and mitigate thermal expansion issues.
Regular Inspection: Conduct regular inspections to identify and replace blades showing signs of wear or developing microcracks.